How do laser cutters work?
We take a closer look at how laser cutters work, as well as the different types available.
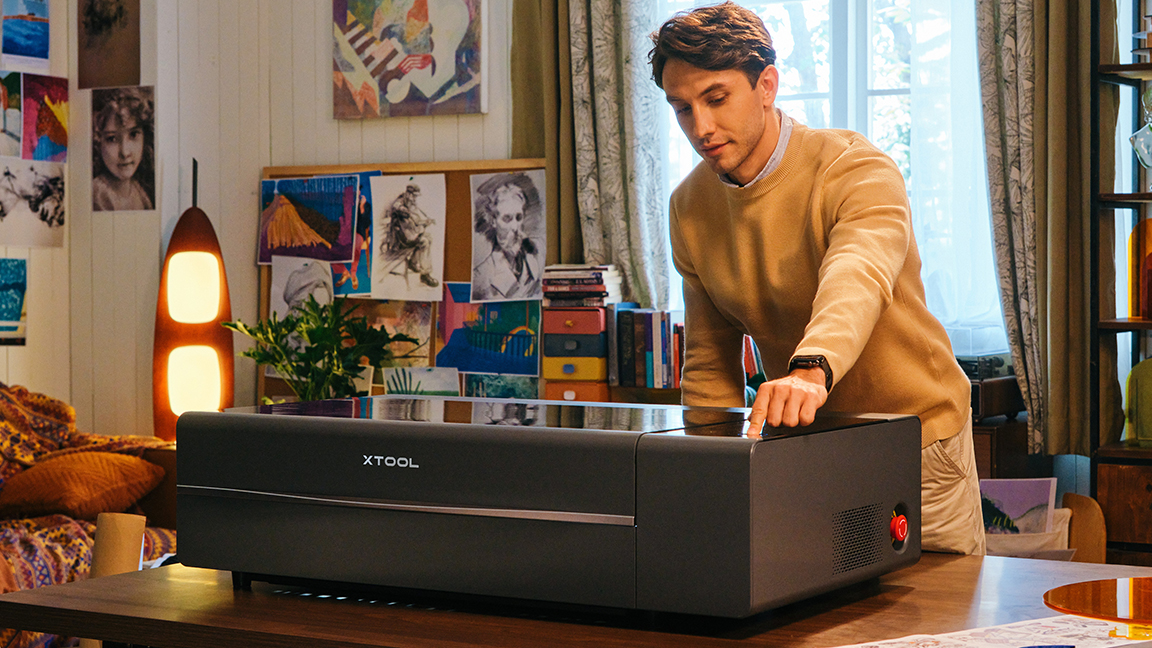
Laser cutters are getting more and more popular among crafters. As a unique means of creating artwork using all sorts of different materials, laser cutting is accessible and fun. If it’s something you’ve been looking into doing – or even something you’ve tried out – you may well be wondering how exactly laser cutting works.
Given that we regularly test and review laser cutters in order to keep our guide to the best laser cutters up to date, we’re pretty well placed to answer this question. This piece is intended to be a quick overview so you can understand the principles behind laser cutting, in order to better help you pick the right laser cutter for you. Let's dive right into it...
1. Laser cutting: the basics
The fundamentals of laser cutting involve creating a narrow beam of focused light. Unlike ordinary light bulbs, which send light out in all directions at once, lasers will use optics to tightly focus the light into a beam powerful enough to melt, burn or vaporise various materials.
The beam is usually infrared or ultraviolet (and therefore invisible), and by directing it using CNC (computer numerical control), the user can etch complex patterns and designs in the material of their choosing. The narrowest point of the beam will be extremely small – generally less than 0.32mm – allowing for high precision. Some cutters will also employ pressurised gas, blowing it into the kerf (the cut) to improve the efficiency and finish.
There are various different types of laser cutters, which we’ll come onto momentarily, and you’ll need to use different ones depending on whether you want to cut into wood, paper, acrylics, metals or whatever else. Depending on the material, the cutter may need to use a high-powered burst to pierce the surface before the cutting proper can begin.
2. Types of laser cutters
The main types of laser cutter are as follows:
Diode laser cutters: These work by using special semiconductor diodes to generate light that is passed through a focusing lens. They’re not as powerful as the other types available, but they are generally very affordable. For cutting soft materials like wood, cardboard, paper, leather and acrylic, a diode laser cutter will work well.
Daily design news, reviews, how-tos and more, as picked by the editors.
CO2 laser cutters: These work by sending an electrical current through a glass tube filled with a mix of gases – mostly carbon dioxide (hence the name) but also hydrogen, helium and others. The current excites the gas molecules, producing light that is then directed into a beam using mirrors. They’re some of the most common types of laser cutter on the market because they are efficient and fairly cheap to make. They’re best with organic materials like wood, as well as acrylics including clear acrylics.
Fibre laser cutters: These are a newer type, using a seed laser to produce a beam that is then amplified in a glass fibre. Their increased power and extremely small spot size allows for them to be used to engrave metals, including reflective metals. They also have no optics, meaning they don’t need to be aligned – however, all this comes at a cost.
Laser cutters come in different physical configurations – open-frame or fully enclosed. The difference is much as it sounds, with open-frame cutters being cheaper and requiring less space to set up, but enclosed ones being quite a bit safer, especially for novice users.
3. Laser cutting software
Laser cutters require the use of multiple types of software. You’ll need to use design software for making up the designs that you want to be laser-cut into your chosen material, and then control software to instruct the cutter to make the required cuts.
Premium laser cutters from known brands like xTool and Glowforge will come with their own bespoke software to streamline the process for you – see our Glowforge engraving tutorial to get a feel for how this works. If you opt for a cheaper cutter, you may need to source third-party software yourself. This isn’t necessarily a bad thing though – there are some excellent programs out there like LaserGRBL, Lightburn and Inkscape, all of which provide intuitive platforms for beginners to learn the ropes on.
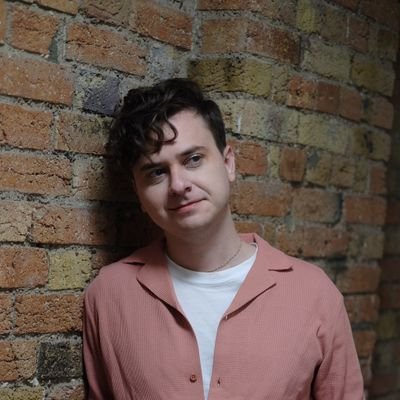
Jon is a freelance writer and journalist who covers photography, art, technology, and the intersection of all three. When he's not scouting out news on the latest gadgets, he likes to play around with film cameras that were manufactured before he was born. To that end, he never goes anywhere without his Olympus XA2, loaded with a fresh roll of Kodak (Gold 200 is the best, since you asked). Jon is a regular contributor to Creative Bloq, and has also written for in Digital Camera World, Black + White Photography Magazine, Photomonitor, Outdoor Photography, Shortlist and probably a few others he's forgetting.