The best print finishes to enhance your work
We take stock of some of the delightful array of special finishes on offer for print products.
Choosing what paper to print a project on can be a dizzying decision given the range of stock available, but that variety is nothing compared to the decorative finishes you can apply on top.
Sure, you could just stick to CMYK – and you can be wildly creative with just those four inks. But if you want to give your work a little sizzle then you should investigate the range of specialist decorative print finishes you can add.
Some techniques, such as UV spot varnishes, die-cutting and embossing will be familiar to many, but there are lots of exotic options, and the printing industry is constantly innovating to develop even more. Even better, you can combine these finishes to create printed products that are completely unique.
Befriend your printer
The first step, as is often the case, is to strike up a working relationship with a printer or specialist finisher. You'll need to know what's possible and how best to prepare your artwork for output, so finding and chatting to a printer is ideal, especially if it's local so you can actually go in and talk through some options.
Computer Arts magazine's finishing partner is Celloglas, but there are many more (some of whom we'll talk to in a moment) so search online for 'decorative finisher' or 'print finisher' to find one that's right for you.
Be aware that it's common to interpret 'print finishing' as trimming, binding and so on, so be careful you're not getting a company that doesn't have the expertise in fancy finishes.
What kinds of fancy finishes?
Some, as we've said, are pretty common. You could, for example, just coat the entirety of a booklet or magazine cover with a varnish – matt, satin or gloss.
Daily design news, reviews, how-tos and more, as picked by the editors.
Or you could just apply the varnish to specific areas, to highlight a masthead or a product, for example. Often, this varnish is dried or 'cured' with ultraviolet light, which is why you'll often hear it referred to as 'UV'.
Previously, printing with white onto black stock would only have been possible using screenprinting, but advances in digital printing mean it’s now possible to achieve a very similar density of white
"Celloglas has a unique machine which can offer two finishes in one pass," says the company's sales director, Steve Middleton. "We can run a spot gloss UV together with a spot matt UV in as fine detail as required."
"We can also offer textured varnish, soft touch varnish, fragranced and rough matt UV, and all of these can be mixed and matched. We also offer a range of unique screen varnishes, such as glow-in-the-dark, photochromic (light sensitive), thermochromic (heat sensitive), glitter varnishes, high-build varnishes and silver latex (scratch-off) – all of which can be combined with other finishes."
Printing trends
Laser and die-cutting are also quite commonplace – your use of which may depend on the size of the print run. And you should think creatively about how you can use that effect, such as die-cutting a design into a cover and setting a plain coloured piece of paper behind it.
Alyson Hurst, a paper consultant at GF Smith, reveals "there's a vogue for kraft paper or natural shades highlighted with strong accents," and combining this fashion with die-cutting can be very effective.
Hurst also points out that duplexing and triplexing – layering up two or three (or more) different papers – are particularly on-trend, as is colouring or foiling the edges of heavy stock.
Foil blocking can look wonderful, of course, especially if combined with embossing or debossing. Although it can be one of the most expensive print finishes, charged according to percentage of coverage.
Celloglas also makes Mirri Board, which is essentially a foil board to which you can apply opaque white and a four-colour process for some spectacular effects. "We can also make bespoke holograms into the Mirri Board, which can be printed to register," Middleton tells us.
Printing opaque white
Printing opaque white – which used to be only achievable with labour-intensive screenprinting, but which is now possible through the use of digital presses – brings exciting options too.
"One of our favourite print processes is the use of digital white on coloured or black stocks to create novel effects at exceptional quality," says Paul Hewitt at Generation Press.
Tactile finishes
Of course, if you don't want a crisp, polished effect, GF Smith's Hurst tells us that Risograph printing "gives a very 'hand-crafted-at-home-by-amateurs' feel to your design work."
"Velvet varnish combined with gloss UV is very on-trend at the moment," says Middleton. "We have a new textured varnish being launched together with 3D varnish, and are currently installing a digital embossing machine which can apply polymers in a high build in exact registration (like Braille); all things that you can touch and feel are very popular."
Of course you can also do embossing and debossing the old fashioned way, pushing designs into or out from your substrate, whether or not you also apply ink, foil or other finishes. Letterpress printing, which is actually the oldest form of printing, gives stunning, tactile results, especially in soft cotton papers.
"Letterpress has had a steady increase in popularity in the UK in the last five or six years, and is hugely fashionable in the USA," Athena Cauley-Yu of Meticulous Ink tells us,
"We tend to print with an impression with our letterpress printing, separating ourselves from the other highly skilled traditional letterpress companies in the UK who tend to use moveable type, and would usually avoid impression due to the risk of damaging the type involved."
Know your timeframe
Whatever finish you choose, check timescales, warns GF Smith's Hurst; they often take longer to produce successfully compared to regular CMYK output.
Generation Press's Hewitt advises keeping it simple: "With the right use of a foil block or a spot UV, a die-cut or a simple embellishment can often be far more effective," he argues.
But if you want to add gold foil blocking to a letterpressed design, printed with white onto dark purple, duplexed stock with some un-inked text printed with a scented varnish, we won't stop you. In fact, that sounds fantastic – why don't you send us one?
Words: Christopher Phin
This article first appeared inside issue 239 of Computer Arts, the world's best-selling creative design magazine. Get up to 55 per cent off a subscription to CA here.
Liked this? Try these...
- How do you choose the right font?
- How to effectively manage your cashflow
- The best collage maker tools – and most are free!
Thank you for reading 5 articles this month* Join now for unlimited access
Enjoy your first month for just £1 / $1 / €1
*Read 5 free articles per month without a subscription
Join now for unlimited access
Try first month for just £1 / $1 / €1
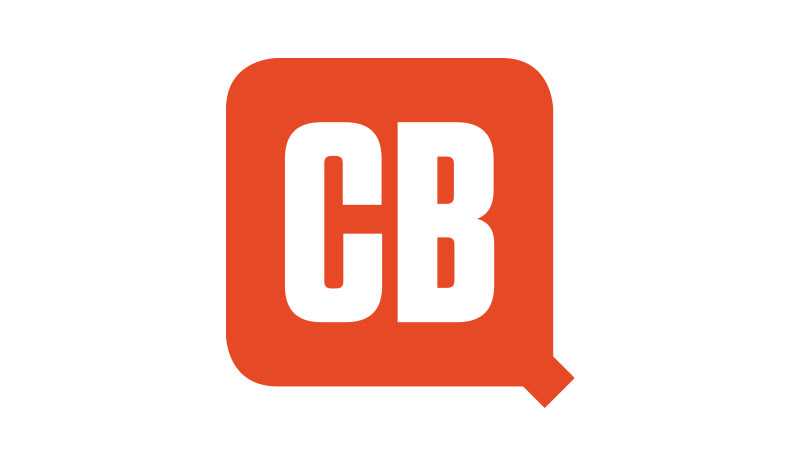
The Creative Bloq team is made up of a group of art and design enthusiasts, and has changed and evolved since Creative Bloq began back in 2012. The current website team consists of eight full-time members of staff: Editor Georgia Coggan, Deputy Editor Rosie Hilder, Ecommerce Editor Beren Neale, Senior News Editor Daniel Piper, Editor, Digital Art and 3D Ian Dean, Tech Reviews Editor Erlingur Einarsson, Ecommerce Writer Beth Nicholls and Staff Writer Natalie Fear, as well as a roster of freelancers from around the world. The ImagineFX magazine team also pitch in, ensuring that content from leading digital art publication ImagineFX is represented on Creative Bloq.